Article: Design World
Semiconductor - Sensor system ensures heat sink efficiency
Heat sinks must efficiently conduct heat away
from the electronic components that generate
this heat. The new Tactilus® heat-sink analysis
system helps you quickly and precisely test
and correct the surface contact and pressure
distribution between the heat sink and its source.
Even a slight warping of the heat exchange
structure or reduction in surface contact area
can have a profound effect on cooling efficacy.
If the pressure distribution is not uniform, heat
conduction will be low, and the electronics may
overheat.
The Tactilus® sensor lets you see actual contact forces and pressure distribution data on the circuit board components. As the mounting screws between the CPU and the heat sink are torqued, the sensor sends signals to map and measure the changing pressure distribution between the mating surfaces. These data are displayed through the software. The heat sink interface can be tested, manipulated, and repositioned in real-time. The sensor also provides the pressure data needed for FEA simulation predictions.
Unlike conventional transducers, this sensor is flexible and 0.015-in. thick (0.38 mm), allowing it to be placed between the CPU and heat sink without affecting the assembly. The sensor pad has 625 resistive sensing points arrayed on a 25 x 25 grid. The total sensing area is 2 in. x 2 in. The scan speed is up to 1,000 Hz, and the operating pressure range is 0 to 100 psi (0 to 7 kg/cm2).
It collects and processes data using Windows-based software that:
- Creates pressure versus time graph and histograms
- Performs 20, 3D and 360 degree image rendering and region of interest scaling
- Displays maximum, minimum, and average pressures and does force integrations
- Prepares reports through export to Excel, ASCII, or Access formats.
The sensor system will endure hundreds of diagnostic uses on different heat sinks with consistent repeatability. It is resistant to electromagnetic noise, temperature, and humidity fluctuations. Accuracy is � 10%; repeatability is � 2%; hysteresis is � 5%; and nonlinearity is � 1.5%.
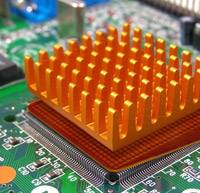
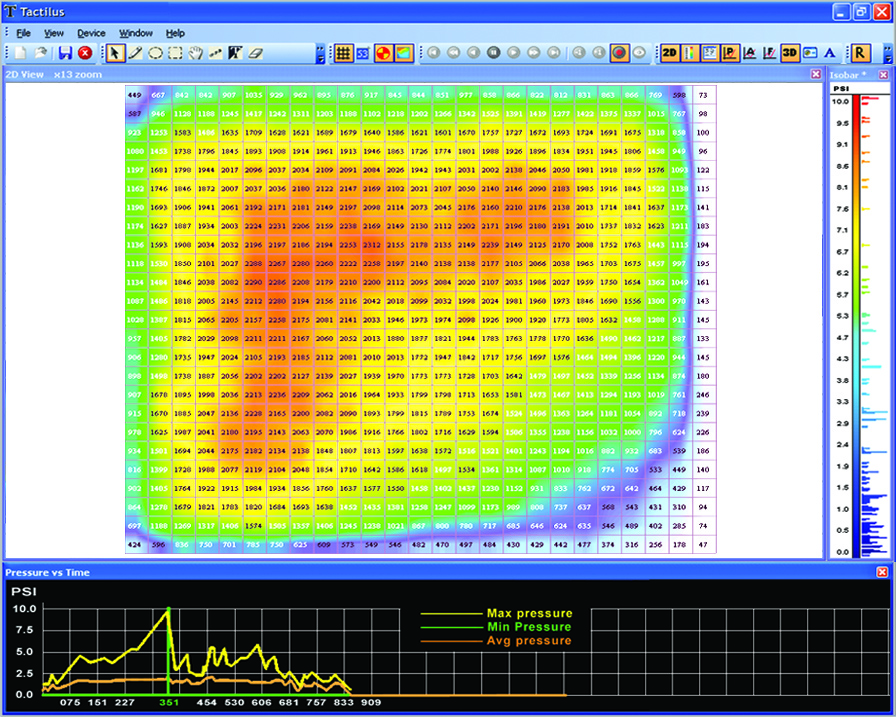